What is the Design Essence of Aluminum Extrusion Dies for Sunflower-Shaped Radiators?
- By:SJHM
- Date:15-04-2025
With the advancement of modern technology and deepening understanding of aluminum alloys, these materials have found increasingly widespread applications. Renowned for their lightweight, aesthetic appeal, corrosion resistance, and superior thermal conductivity and formability, aluminum alloys are extensively utilized in IT, electronics, automotive industries, and particularly as heat dissipation components in the LED sector. While these aluminum heat dissipation products excel in performance, their production poses challenges. High-efficiency extrusion molding is critical for such radiator profiles, which typically feature numerous densely packed fins and long cantilevers. Traditional flat dies, split dies, and semi-hollow extrusion dies struggle to address issues related to mold strength and shaping precision. Consequently, manufacturers often rely on costly imported steel to enhance mold durability, yet average mold lifespans remain below 3 tons, driving up radiator costs and hindering LED adoption. This has spurred significant interest in extrusion dies for sunflower-shaped radiators. Drawing on years of research and practical trials, this article introduces innovative technical solutions for optimizing these specialized dies.
aluminium al 6061
aluminum alloy 6063
1. Structural Analysis of Radiator Profiles
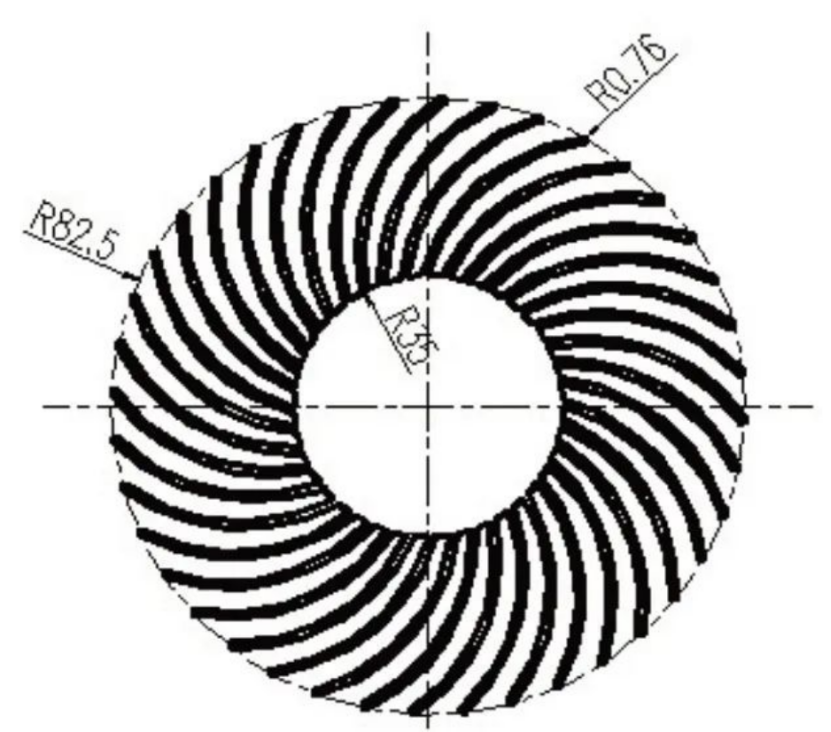
Figure 1: Cross-section of a typical sunflower-shaped radiator aluminum profile.
aluminum fabrication
aluminum company
product manufacturing
The profile shown above has a cross-sectional area of 7,773.5 mm² with 40 fins, resulting in a maximum cantilever opening of 4.46 mm and a calculated tongue ratio of 15.7. The central solid section spans 3,846.5 mm², contributing to structural complexity. Each fin-cantilever unit functions as a semi-hollow profile, demanding exceptional mold strength. Unlike conventional semi-hollow dies (e.g., cover-type, cutting-type, or suspension-bridge dies), sunflower radiators require tailored solutions to balance metal flow and reduce extrusion forces. Excessive flow rates in the central solid zone can induce tensile stresses at fin roots, risking fracture. Thus, optimizing metal flow distribution is critical for enhancing mold durability.
aluminium alloy
2. Die Structure and Extruder Selection
2.1 Die Structure
A split die with upper weld chamber is recommended (see Figure 2). This design features modular inserts for cost efficiency and rapid prototyping. The upper and lower die sleeves are standardized, while precision-machined inserts ensure accurate bearing zones. A stepped lower die cavity (interference fit at the base and clearance fit at the top) guarantees concentricity and ease of assembly, mitigating deformation risks.
aluminium and aluminium
aluminum manufacturers
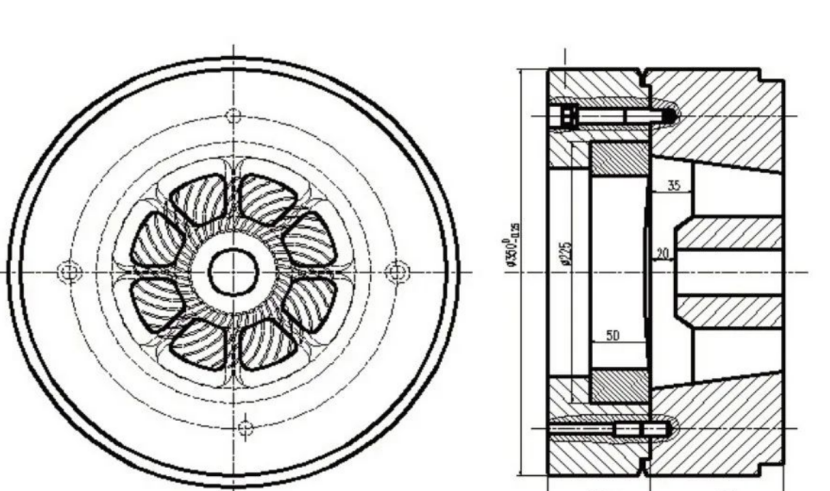
2.2 Extruder Capability
For the profile in Figure 1, a Φ208 mm extruder with 20.0 MN capacity was chosen, yielding a maximum specific pressure of 589 MPa—optimal for balancing force requirements and tool life. Industry guidelines suggest a compression ratio <25 to avoid excessive stress on fins. Calculated extrusion coefficients and specifications (e.g., Φ350 mm × 200 mm die dimensions) further ensure manufacturability.
aluminum heatsink
3.Critical Manufacturing Techniques
While CNC machining aligns with standard practices, electrical discharge machining (EDM) demands specialized protocols:
Wire EDM:
Prevent electrode deformation by pre-grinding copper blocks, calibrating perpendicularity, and using incremental cutting paths.
Trim electrodes post-machining to eliminate residual stress.
EDM Finishing:
Optimize current settings (7–10 A for roughing, 5–7 A for finishing) for surface quality.
Ensure uniform clearance between fins and die walls through iterative adjustments.
Maintain electrode alignment and cleanliness to avoid defects like misaligned air gaps or perforated bearing zones.
anodized aluminum
4. Key Design Principles:
Flow Optimization: Limit bridge widths to ≤16 mm and ensure split ratios exceed 30% of the compression ratio.
Material Selection: Use premium hot-work tool steels with triple-vacuum heat treatment for enhanced wear resistance.
Conclusion
Successful production of sunflower radiators hinges on meticulous design, precision manufacturing, and material science. By prioritizing stress reduction, flow control, and thermal management, manufacturers can achieve mold lifespans exceeding industry norms while reducing costs. For further insights or collaboration, Contact shijun hongmao aluminum, your trusted partner for custom aluminum profile manufacturing. With 20+ years of expertise, we provide one-stop services from precision deep processing to complex extrusion solutions, delivering high-performance aluminum products for global industries.
Custom Aluminum Extrusions & Profiles Manufacturer
Profile Custom Extrusions
Custom Aluminum Extrusions Service
Profile Precision Extrusions
Custom aluminum extrusions
Aluminum extrusion manufacturers in china
decorative aluminum
Aluminum bracket
uchannel aluminum
extruded aluminum heatsink
aluminum components
aluminum housing
Aluminium Decorative Strips